Getting a perfect edge on a blade depends on a few factors such as; blade steel, thickness, degree of the sharpening angle, and the condition of the blade. After taking these factors into consideration, you also need to look at what media will be used to sharpen or hone the blade’s edge. If you properly care for your knives (or edged tools) there shouldn’t be a need for a coarse stone such as a coarse diamond, silicon carbide, or aluminum oxide material. To get that razor-sharp edge I personally use Arkansas oil stones.
The stones being tested in this article are from Hall Sharpening Stones (formerly Hall’s Arkansas Oil Stones), a R.H. Preyda Company. Before this test and evaluation begins, I wanted to share some information about this company. They are looking to expand their facilities, bring in new machining and tooling, and may be expanding their product line to include more specialty items such as the possibility of gunsmith specific stones and sets. All of this information definitely has peaked my interest, and I’m looking forward to seeing what this manufacture has planned down the line.
For this T&E, I used AUS-8 (SOG Trident Tanto, Cold Steel Bird & Trout, SOG Flash 1), 420 stainless (SOG Fasthawk), 440C stainless (Benchmade Rescue Hook), and carbon V (Cold Steel Recon Tanto). The bench stones I used are the soft (medium), hard (fine), and surgical black (extra-fine) Arkansas stones. For the Rescue Hook and the serrations in the Flash 1, soft and surgical black slip stones were used. The angels I personally set the blades at vary. While most of the time a 22 degree angle is used as a rule of thumb, I found that angling the blade up a distance equal to the thickness at the rear of the blade works well for my purposes (this is the method I used).
Looking at the stones I realized that this company’s products are excellent. The edges of the stones are a crisp 90 degree angle, and they had a perfectly flat surface on all sides. The slip stones have the same attributes, and offer multiple angles to work with (great for serrated, curved, or different shaped blades and tools). The honing oil was of a light consistency, and produced a slick surface on the stones. These stones were also drop tested from three feet. A word to the wise; as expected, handle them with care and don’t drop them to maintain a precise edge on the stones.
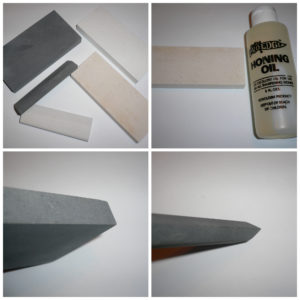

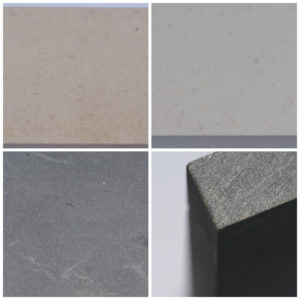
Using the stones in the order of soft, hard, and surgical black work by removing the micro serrations (which lead to rapid dulling) left by use or a rougher sharpening material. By honing and polishing the blades, the end result is a consistent edge that resists dulling and provides a smoother cut. The following images contain the results of the tests along with the “paper cutting test” that shows the progress of each step, and were conducted with ten passes (with each stone) on each side of the blade with the exception of the Rescue Hook and the serrations on the Flash 1. The area of focus is the edge of the blade and with this in mind, look for the honing of the cutting surface. The images are organized to show the progress of each stone, and should be viewed: Top left; original edge, Top right; soft stone, Bottom left; hard stone, and Bottom right; surgical black stone.
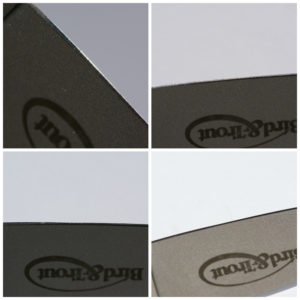
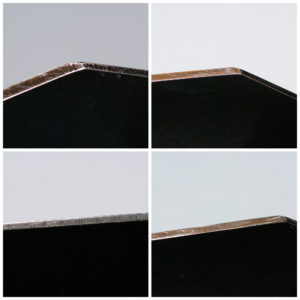
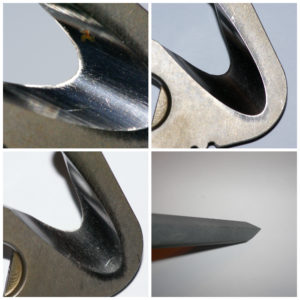
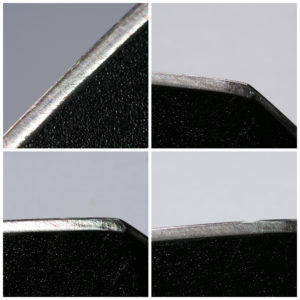
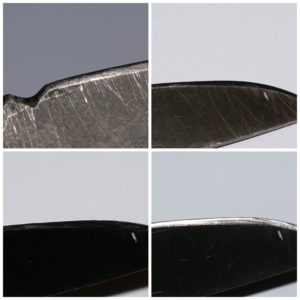
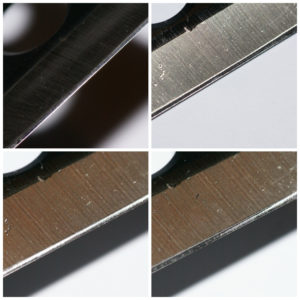
After using each stone on various types of steel I conducted the “paper cutting test”, using only the weight of the knife or tool as I drew back. The goal was to show the progress and blade refinement of each step. I found that the products from Hall Sharpening Stones worked the blade in a manner that left each edge polished and burr free. Using a small amount of pressure provided these great results, and there was no visible wear on the stones. The designations in the photographs are as follows: Pre; previous or original edge, #1; soft stone, #2; hard stone, and #3; surgical black stone. Due to only two slip stones being used on the Rescue Hook, the test is shown as: Pre; previous or original edge, #1 soft slip stone, and #2; surgical black slip stone.
After viewing the results and examining the stones and blade edges after testing, I am happy with Hall Sharpening Stones. The products used in this article are of top shelf quality, and (in my opinion) are worth the price. This proud company offers many different styles, sets, and varieties of Arkansas stones that fit a number of applications. In the throwaway society that we live in, it’s nice to see a company dedicated to helping us maintain the knives and tools that we spend our hard-earned money on. Let’s face it, if you want quality it’s worth the investment on such items. The same is true with their upkeep. I’m really looking forward to acquiring more great products from this company, as well as any new ones that may become available. The bottom line is: Hall Sharpening Stones is a one stop shop for all of your knife and tool maintenance needs.
Thanks for reading,
-Rhody
You must be logged in to post a comment.